I.Background of the Project
Featured with short construction period and fast startup, the ratio of gas turbine power plants in global power production industry has turned more and more important. For dealing with the wide ranged accident in electricity transmission network and recovering power supply, the gas turbine power plants, especially those can black-start, have become more important.
The 1st stage of construction in Gaili Power Plant of Sudan equipped the plant with 2 sets of 206B gas turbine ¨C steam combined cycle equipment (including 4 gas turbines), making the plant black start possible, and under 40 degrees centigrade, power output being 200MW; the plant started supplying power in 2003 and being put into full production in 2004. The plant¡¯s load was one third of the Sudan grid loads that time, so it wasever a gigantic enterprise only next to Khartoum Refinery in Sudan. Even the president had taken part in the plant¡¯s commence ceremony, meaning its importance in the country.
However, with the expansive constructions on Merowe hydropower 1250MW and Karbe Power Plant Stage 2 200MW in Sudan, as well as the followed in-service of Gaili Power Plant Stage 4 110MW (fuelled by refined oil and coke), ratio of the Gaili Power Plant Stage 1 has become lower and lower, and meanwhile, Gaili Stage 1 is fuelled with LDO and LPG, but due to price climbing in global petrol market, its cost has turned much more expensive, causing the power plant retreated from the main force of power supply, and finally becoming a peak adjustment equipment, being much less important.
The only way to the power plant is to seek for further development, decrease fuel cost and look for a usable fuel with lower cost. Khartoum Refinery, a neighboring enterprise to the power plant, can supply heavy coked gas oil, abbreviated as HCGO, a medium product made in refining process, which costs one third of LDO. Whether the fuel could be used and how, the owner had no idea, but Nangang Power, accumulating rich experiences in fuel renovation for gas turbines, had renovated light oil to heavy oil for lower cost in early years, and in recent years, in order to decrease pollution and satisfy the needs of environment preservation, has executed the renovation of oil to NG, and the renovation of LDN combustion system for decreasing emission of NOX recently, totally renovating the gas turbine sets numbered close to 50 sets.
After comprehensive consultation, the owner chose Nangang Power to execute the renovation for the four turbine sets in the power plant stage 1, and in July, 2012, signed contract.
II.Design of the project
1.Basis
1.1.Fuel composition and performance
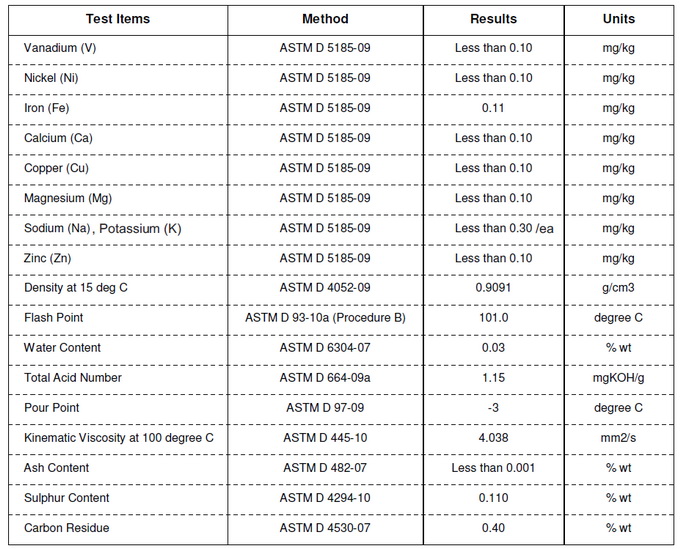
1.2.Fuel viscosity
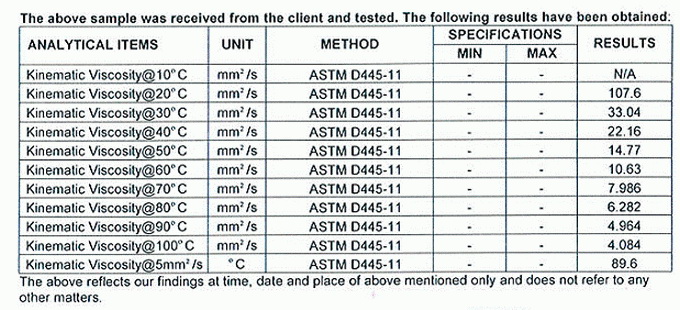
1.3.Miscellaneous
Owner power plant¡¯s design drawings, files, turbine maker¡¯s drawings, files, and owner¡¯s other needs.
2.Design scale of the project
All renovated and added equipmentfrom oil tank to turbine include:
2.1.Oil tank zone: Add 1 oil tank heater and piping of the oil tank zone;
2.2.Pump chamber zone: Add 4 fuel transmitting pumps, 4 heaters and their piping, and one fuel oil pump chamber;
2.3.Gas turbine zone: Add 4 filter selection skids and 1 HCGO flush oil-return tank;
2.4.Piping corridor zone: Connect the fuel oil pipes and their steam and meter air pipes between the pump chamber and the filter selection skid;
2.5.Turbine body: Replace atomizing air pumps, flow dividers, and fuel one-way valves, and add fuel flushing valves and related piping;
2.6.Controlling and electrical: Add related controlling and electrical systems for the target of safe turbine running.
3.Design of the system
Based on the analysis report of the fuel oil selected by the owner, contents of Na, K, V, Ca, Pb (not inspected) don¡¯t exceed the requirements in GE gas turbine instruction GEI-41047K, so the fuel is free from treatment on Na, K, V, Ca or Pb, but regarding the fuel viscosity that cannot reach direct use, it can be solved by heating the fuel to satisfy requirement of the gas turbine.
3.1.Schematic diagram of design:
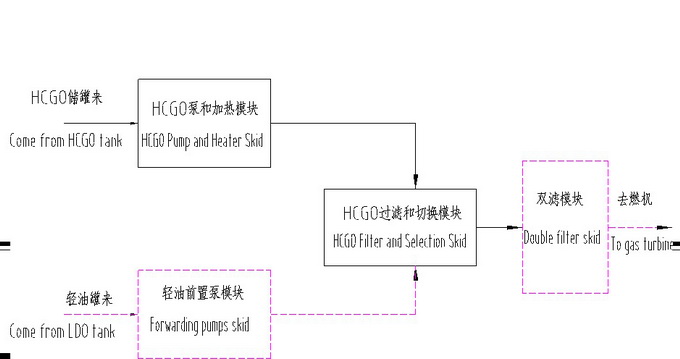
The LDO sent from the LDO pump flows from Y filter YF101, normally closed pneumatic ball valve VA103, flow meter FM103, self-rising pressure change valve RV101 to the 3-way selection valve, and before its entrance into the selection valve, the LDO pressure after the self-risingvalve RV101 is adjusted to be a bit higher than HCGO by the valve RV101.
3.2.5.Piping
The old LDO piping in the power plant is dual header manifold, but in the renovation project, one LDO manifold will be reserved and another one will be reconstructed into the oil return pipe for the HCGO, and one more fuel pipe for HCGO will be added.
The HCGO heating steam is taken from the old LPG heating steam in the power plant; a 3-way path is installed on the manifold of LPG heating steam, leading the steam into the heater in the pump chamber to heat HCGO.
The steam pipes and HCGO pipes require heat preservation, so air drain valves are settled on the top point, dirt drain valve are settled on the bottom point, and water drain valves are settled on the lower position of the steam piping.
On the farthest end of the fuel header manifold, a pneumatic pressure change valve PCV501 (normally opened) is settled to retain the header manifold pressure at 4 bars. The PCV501 itself is installed with a positioning controller (including the air source filtering and pressure changing); in accordance to the DCS comparison between the set and the pressure signal measured by pressure transmitter 96PF-1, 4-20mA signal will be given to the valve locator to control valve openness, in order to change the pressure in HCGO header manifold by means of changing the HCGO oil return volume.
3.2.6.Turbine body
After renovation to HCGO, the turbine body is required corresponding reconstruction:
Fuel flow distributor: Replace with a new fuel flow distributor to adapt to the HCGO operation under high temperature.
Atomizing air pump: Replace with high pressured atomizing air pumps to adapt to the HCGO high viscosity.
HCGO flushing system: Due to high viscosity in HCGO, the pipes will be blocked if the HCGO is cooled and condensed in the pipes, and therefore, if trip and shutdown happens while the turbine is combusting the HCGO, the pipes in the front of fuel nozzles should be flushed, and the fuel oil pipes are flushed by LDO till there is 100% diesel in the pipes, which can be observed by glass sight port.
Turbine wash: Add turbine wash system. The wash pipe is directly divided from the old air compressor wash pipes, passing from the atomizing air manifold, fuel nozzle to the turbine.
3.2.7.Controlling and electrical parts
In order to meet above needs of functions, the disposable meters and electrical equipment are added correspondingly, and the MARK V and DCS programs are revised accordingly.
Four sets of HCGO fuel pumps and three sets of ventilators are added in the new pump chamber, and two rows of electrical controlling cabinets are added in the old MCC chamber.
III.Construction of the project
1.Products manufacturing
After the contract was put into effect in July, 2012, Nangang Power started product design, and in late July, finished the drawings and preliminary design, and delivered them to the owner for evaluation; On Aug. 11, Nangang staffs flied to Sudan to take part in the design contact conference, answering various questions put forward by the owner, and through comprehensive discussion, the final design plan was decided.
Then Nanjing Nangang Power swiftly organized long period of equipment procurement, and in the meantime, started designing skid drawings; by Sep., we had started making the equipment and skids, including: oil tank heaters, pump and heater skids, and filter and selection skids.
Oil tank heater parts:
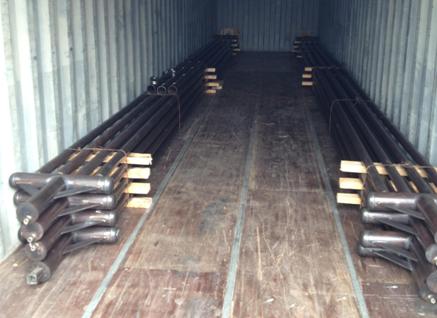
Pump and heater skids:
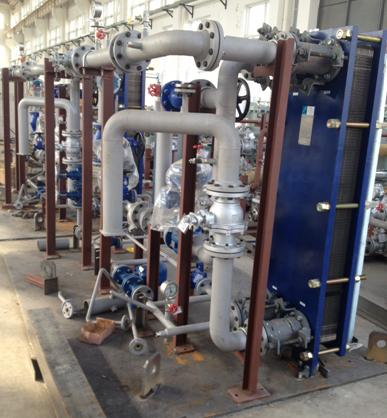
The filter and selection skids in the progress of making (selection valves had not arrived for installing):
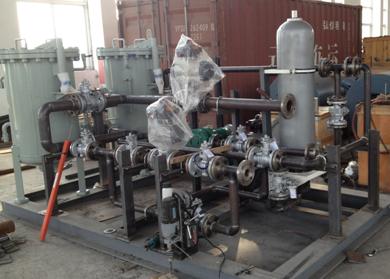
In middle Dec., 2012, the manufacturing production for all of the four sets of renovated equipment, as well as the procurement, checking and accepting of the field installing equipment and materials were completed, which were packed in late Dec. 2012, shipped in Jan. 2013 from Shanghai seaport, arrived at the field of Sudan in middle Mar., 2013, and on Mar. 28, 2013, the field construction of the fuel renovating project was formerly started. 2.Field construction The Gaili Power Plant of Sudan is located at a development zone 80 Km north to Khartoum, neighboring to the Khartoum Refinery invested and constructed by CNPC. Khartoum, the capital of Sudan Republic, is located at the place where the Blue Niles and the White Niles converge. The city is known as the Stove of the World, featured with hot dry weather, yearly average temperature 28.7¡æ and 47.2¡æ the extreme record. From every March to November, when people step out of home, waves of hot air are coming straight on the face, like in a sauna room; usually walking at 10:00 pm, people can feel that the hot air on the ground has not yet left. April and May are the days ravaged by the sand storm from the Sahara;roaring gales rise sands and dusts curtaining the whole place, which can be undergone for several days. The sands all over the sky can invade everywhere, and even at indoors, the muddy taste is smelt constantly; sometimes you can be suffocated to wake up from the dream. The renovating project was meeting the hottest season in Sudan; baked by the malicious sun, grasses and plants had to yield and bow themselves; a puppy was retreating to a place beneath a cooling tower, laying down, and letting its tongue put out, gasping. Nangang Power staffs, however, were working tenaciously for the construction project under the fierce Apollo, and many of them were sunburned and suffered from blisters and peeling. On the morning shift, at the moment of starting the work, their working cloths seemed to be submerged in water immediately, but baked dry soon by the sun, causing the cloths to turn hard and wear out their skin due to complete immersion of the white salty stains into the textile. Under such a hard condition, Nangang Power completed the constructing missions earlier than schedule, with quality and workload guaranteed. On July 2, the fuel switch for the first gas turbine set was smoothly completed, and the turbine was running in steady fuelled with the HCGO; on July 5, the 72-hour test running was completed. The no.2 gas turbine fuel switch was smoothly completed on July 6, and on July 9, the 72-hour test running was finished. The no.1 and no.2 gas turbines were in steady operation, with all items in normal. After June the Niles valley turned drought and the water level lowered, so the hydropower load decreased substantially, and besides, due to the overhauling for the turbine sets in Karbe Power Plant, the loading matter on the grid was emergent, and therefore, the shutdown for reconstruction of the no.3 and no.4 gas turbine sets was not approved by the grid company of Sudan, and those turbine bodies¡¯ renovation was not completed on time, leaving the missions continue till the rainy season. Thus, on July 11, all Nangang Power constructing personnel left Sudan, waiting for the moment when the no.3 and no.4 turbine sets stop their service in the grid, and then we will back to Sudan for the rest work. The piping in construction: ¡£
The piping in construction:
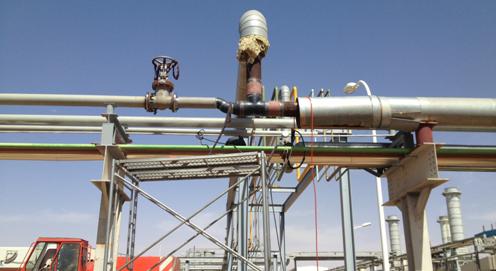
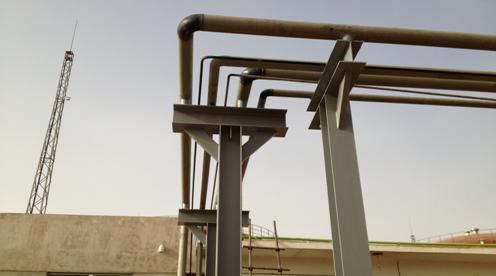
Install the pump chamber equipment at the late period of the construction:
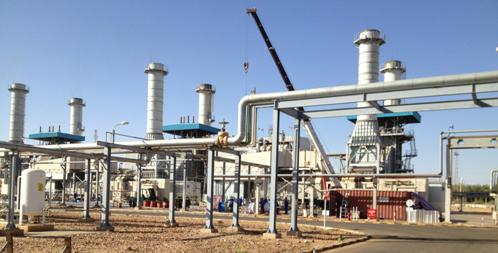
Nangang Power personnel and the owner in adjusting and testing:
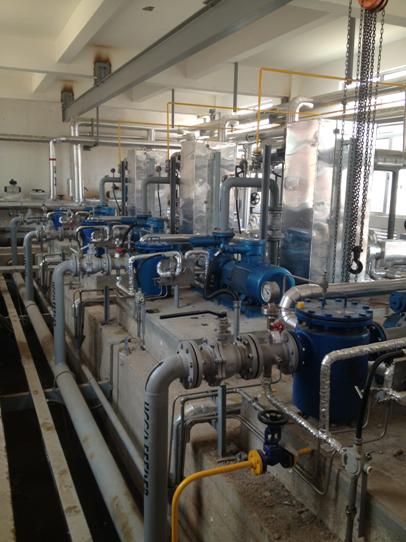
The piping corridors in field construction:
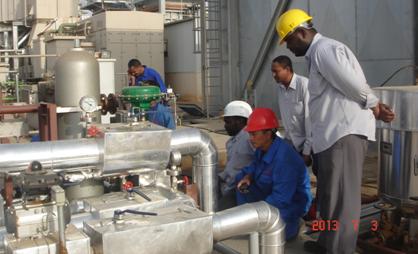
Nangang personnel entered into the field of Sudan again in middle Dec., the best season in Sudan, comfortable in weather and large in daytime and evening temperatures, which is ranged in 10 to 35 degrees centigrade, much comfortable than the first mission to Sudan when the temperature in most days had been over 45 degrees centigrade. On Dec. 12, the no.3 and no.4 turbine bodies reconstruction, as well as the replacement of heaters at the exit of oil pumps, followed by add of oil return piping, were started. On Jan. 12, 2014, all of the fuel renovating construction, adjusting and testing items were completed.
From the oil tank heaters to the turbine bodies, all of the equipment in the reconstruction, include the oil pumps, heat exchangers, and the systems of pressure change, temperature change, and selection, were operating normally, reaching the expected and designing targets, bringing about profitable effect to the owner, and being commended by the owner